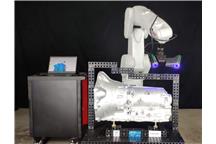
Zastosowanie inżynierii odwrotnej maszyn, części urządzeń i narzędzi odgrywa kluczową rolę w wielu dziedzinach przemysłu, na przykład w branży produkcyjnej, lotniczej, motoryzacyjnej czy elektronicznej. Przynosi szereg korzyści, usprawniając proces tworzenia parametrycznego modelu CAD, produkcji części zamiennych, inspekcji jakości wyrobów, wdrażania ulepszeń w obrębie komponentu i nie tylko.
Na czym polega inżynieria odwrotna maszyn i co można dzięki niej stworzyć?
Inżynieria odwrotna maszyn, części i narzędzi polega na nadawaniu postaci cyfrowej różnego rodzaju realnym obiektom, a także zestawom przedmiotów. Dzięki skanowaniu laserowemu 3D uzyskać można komputerowe, trójwymiarowe modele umożliwiające między innymi:
- wspomaganie procesów wytwarzania CNC, druku 3D itp.,
- przeprowadzenie analizy geometrii lub wymiarów obiektu,
- wykonanie symulacji komputerowej i produkcję tego samego przedmiotu o innych parametrach,
- kontrolę wydajności czy zgodności narzędzia, części maszyny lub urządzenia.
Przypadki, kiedy inżynieria odwrotna jest wyjątkowo przydatna
Obecnie wiele zakładów z branży przemysłowej sięga po rozwiązanie, jakim jest inżynieria odwrotna. Zastosowanie tej technologii jest szczególnie korzystne, kiedy należy odtworzyć wieloletnie narzędzie lub część maszyny pozbawioną modelu CAD czy dokumentów z danymi technicznymi, a także, gdy istnieje potrzeba przeprowadzenia regeneracji uszkodzonego komponentu, który nie jest już wytwarzany przez producenta. Doskonałym tego przykładem może być stworzenie odpowiednika zardzewiałej pokrywy, wyeksploatowanego wirnika bądź korpusu pompy wodnej.
Ponadto inżynieria odwrotna znakomicie sprawdza się do identyfikacji słabych punktów konstrukcyjnych, jak również opracowywania rozwiązań usprawniających działanie na przykład linii produkcyjnej, turbiny wodnej i nie tylko. Dzięki niej możliwa jest optymalizacja komponentów tak, aby działały wydajniej oraz dłużej niż ich pierwotne odpowiedniki.
Korzyści stosowania inżynierii odwrotnej maszyn, części maszyn, narzędzi
Użycie skanera 3D renomowanej firmy, takiej jak SCANTECH, pozwala na odtworzenie obiektu z dokładnością do nawet 0,02 mm, a tym samym uzyskanie wysokiej jakości cyfrowego modelu trójwymiarowego pozbawionego jakichkolwiek braków w danych. Taka precyzja ma kluczowe znaczenie w inżynierii odwrotnej narzędzi, maszyn oraz części urządzeń, ponieważ pozwala na szczegółową analizę konstrukcji w celu ich optymalizacji.
Dzięki temu inżynierowie mogą tworzyć nowe projekty ulepszonych komponentów, bazując na modelach starych części. W wyniku wdrożenia zmodernizowanych elementów osiągalne jest między innymi:
- zwiększenie wydajności maszyn i efektywności produkcyjnej w zakładzie,
- podniesienie elastyczności w zakresie wytwarzania artykułów,
- uodpornienie elementów konstrukcji na usterki,
- poprawa jakości finalnego produktu,
- zwiększenie konkurencyjności przedsiębiorstwa w danej branży.
Warto zaznaczyć, że inżynieria odwrotna w ramach modelowania adaptacyjnego umożliwia też projektowanie w realnym otoczeniu, co zdecydowanie usprawnia proces wprowadzania na bieżąco poprawek w budowie maszyn, komponentów lub narzędzi. Ma to wiele zalet i bez wątpienia prowadzi do postępu technologicznego, pozwalając na rozwój oferowanych produktów. Umożliwia firmom szybkie reagowanie na zmieniające się trendy i potrzeby rynku w zakresie wydajności, jakości oraz innowacyjności.
Kategoria komunikatu:
Inne
- Źródło:
- Materiał nadesłany do redakcji

Czytaj także
-
Zadanie: wybór klimatyzatorów
Klimatyzacja ma kluczowe znaczenie dla prawidłowego funkcjonowania nowoczesnych linii produkcyjnych. W przypadku niewłaściwego...
-
Kluczowa rola wycinarek laserowych w obróbce metali
www.automatyka.plWycinarki laserowe zrewolucjonizowały przemysł obróbki metali, oferując niezwykłą precyzję i efektywność. Dowiedz się, dlaczego są one...
-
-
-
-
-
-