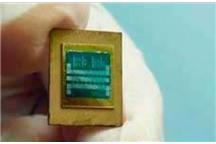
Wydajne podzespoły elektroniczne mają oczywiste tendencje do przegrzewania się. Dzieje się tak, ponieważ wiele komponentów elektronicznych zostaje zespolonych w jednym układzie z taką gęstością, że brakuje w nim przestrzeni na odprowadzanie powstającego podczas ich pracy ciepła. Przegrzanie komponentów elektronicznych może skończyć się często w nieprzewidziany, a nawet tragiczny sposób, w konsekwencji czego zarządzanie emitowanym ciepłem stało się bardzo ważnym aspektem ich projektowania.
Odprowadzanie energii cieplnej jest szczególnie istotne w urządzeniach wykonanych z azotku galu. Materiał ten jest zdolny do przenoszenia wysokich napięć, przez co poszerza możliwości technologiczne zasilania układów dużych mocy. Jednak w tranzystorze wykonanym z azotku galu, ciepło koncentruje się w malutkich punktach, tworząc kilka obszarów ciepła ograniczających możliwość jego praktycznego wykorzystania.
Yong Han z singapurskiego A*STAR wraz ze współpracownikami wykazał zarówno doświadczalnie, jak i numerycznie, że warstwa diamentu umieszczona na powierzchni układu elektronicznego może rozprzestrzeniać ciepło punktowe na większą powierzchnię, poprawiając wydajność urządzeń wykonanych z azotku galu.
Badacze stworzyli układ cieplny scharakteryzowany przez osiem punktów cieplnych, z których każdy posiadał rozmiar od 0,3 do 0,45 milimetra. W ten sposób udało im się zasymulować zachowanie układu elektronicznego z azotku galu. Następnie związali go z warstwą diamentu o wysokiej czystości przy użyciu techniki zwanej chemicznym osadzaniem parowym. Radiator w postaci diamentu został następnie trwale połączony z chipem w trakcie procesu kompresji termicznej. Taka struktura została ostatecznie podłączona do microcoolera z wyżłobiononymi miniaturowymi kanałami, w których swobodnie mogła przepływać woda, odbierając niechciane ciepło.
Han testował urządzenie, generując w układach testowych o grubości od 100 do 200 mikrometrów od 10 do 120 Watów mocy grzewczej. Warstwa diamentowa w połączeniu z microcoolerem była w stanie utrzymać temperaturę struktury układu w granicach 160°C. Jej maksymalna wartość okazała się być o 27,3% niższa niż w przypadku wykorzystania miedzi i o 40% mniejsza niż w sytuacji, w której nie wykorzystywano żadnej warstwy rozprowadzającej ciepło.
Wyniki doświadczalne były następnie potwierdzone przez symulacje cieplne. Wskazują one na to, że wydajność może być dalej optymalizowana poprzez zwiększanie grubości warstwy diamentu i polepszenie jakości połączenia pomiędzy układem z azotku galu a diamentowym radiatorem. Han ma również nadzieję, że w przyszłości uda mu się wraz z zespołem opracować nowy rodzaj microcoolera, który podniósłby wydajność urządzenia na jeszcze wyższy poziom.
(rr)
Kategoria wiadomości:
Nowinki techniczne
- Źródło:
- sciencedaily

Komentarze (0)
Czytaj także
-
Oddziaływanie na środowisko spalarni odpadów
Spalanie odpadów od lat budzi wiele kontrowersji oraz protestów społecznych. Protesty te, wystąpiły praktycznie we wszystkich krajach Europy, a...
-
Kluczowa rola wycinarek laserowych w obróbce metali
www.automatyka.plWycinarki laserowe zrewolucjonizowały przemysł obróbki metali, oferując niezwykłą precyzję i efektywność. Dowiedz się, dlaczego są one...
-
-
-
-
-